Med den bedste robotteknologi vil vi også gerne levere til dig.
Five to one - automation and digitization thanks to smart connection of robots and motors
Innovative and economical solutions usually emerge when people think outside the box. When it comes to automation, this often means combining individual production steps so that workpieces pass through several production stages automatically. The smart networking of individual systems also enables predictive maintenance, monitoring the condition of production equipment and checking production data. The ability to integrate a driverless transport system for picking up and fully automatically transferring the finished parts to the next production step completes the future-proof overall solution.
- Industries
- Metal
- Applications
- Material Handling
- Client
- EGS Automation GmbH
- EGS Automatisierungstechnik
- Products
- GP7 - GP-serie
Five to one - automation and digitization thanks to smart connection of robots and motors
Dunkermotoren, an AMETEK brand based in Bonndorf in the Black Forest, has been developing and producing drive solutions up to 5 kW output power for over 70 years. The manufacturer's modular product strategy allows its brushless and brush DC motors to be combined with gearboxes, encoders, brakes and electronics to create a complete drive solution. The majority of the 1,300-strong company's drive components are manufactured at its headquarters in Bonndorf. For Dunkermotoren, intelligent manufacturing solutions and consistent automation of processes are essential foundations for the competitiveness and quality of its products on the international market.
This can be illustrated by the automation of end shield machining, which was developed and implemented by EGS Automation in 2021. The end shield is the front cover of an electric motor from which the drive shaft protrudes. EGS Automation from Donaueschingen has been supplying Dunkermotoren with robot and automation solutions since 2013. The robot specialist has been developing both standardized machine loading systems and customer-specific special solutions since 1996 and specializes in the automation of manufacturing processes in the metalworking industry.
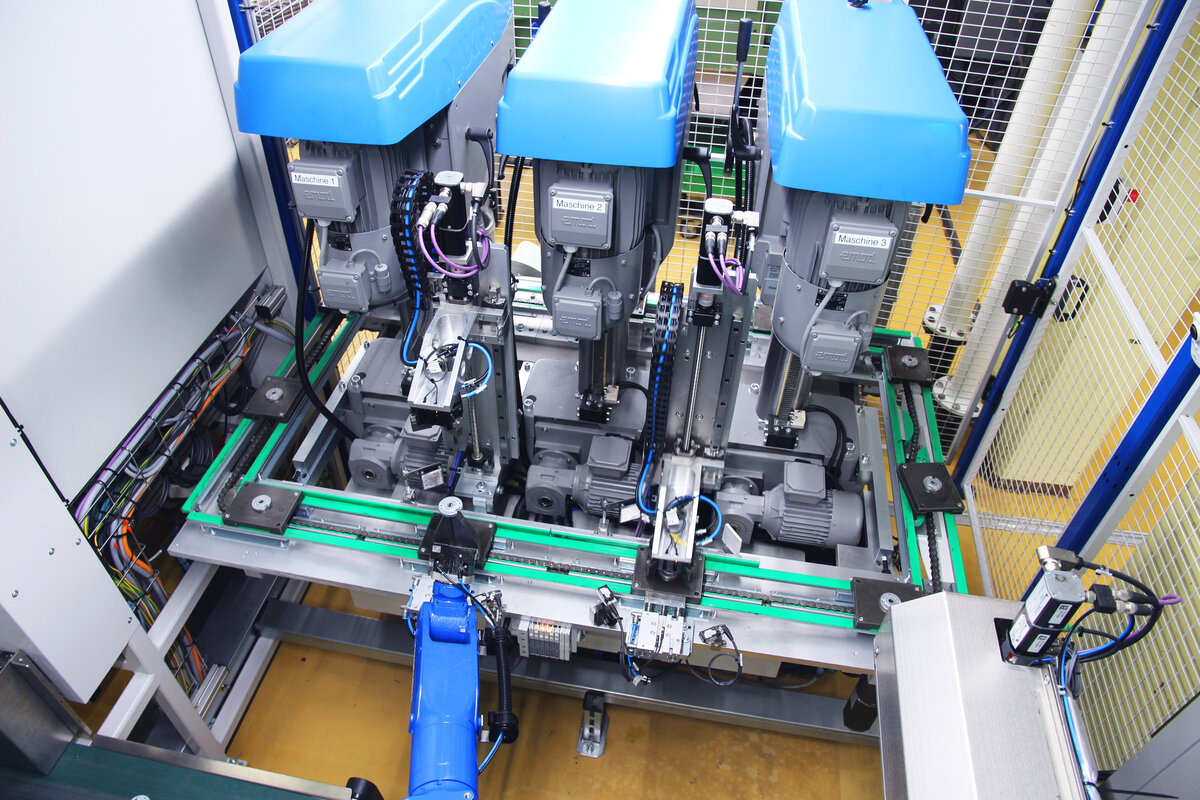
The production process at a glance: Bearing shield machining
Before automation, the end shields at Dunkermotoren were processed in five operations. Each of these operations was an individual workstation where the end shield was inserted into a machine and removed again after machining. This was followed by manual transport to the next work step. The entire process was thus "difficult to plan and involved a high level of manpower", says Mustafa Koyun, Manager Segment GP Production Parts at Dunkermotoren. Two end shield sizes are machined, of which there are a total of ten variants. The machining includes the drilling of holes and threads, as well as the machining of the inner and outer fit, where the end shield is screwed into the motor housing. Depending on the variant, another recess - internal or external - must be turned on the zinc die-cast component. In addition to the mounting holes in the end shield and the radial holes for screwing into the housing, a final threaded hole is required at some variants for grounding.
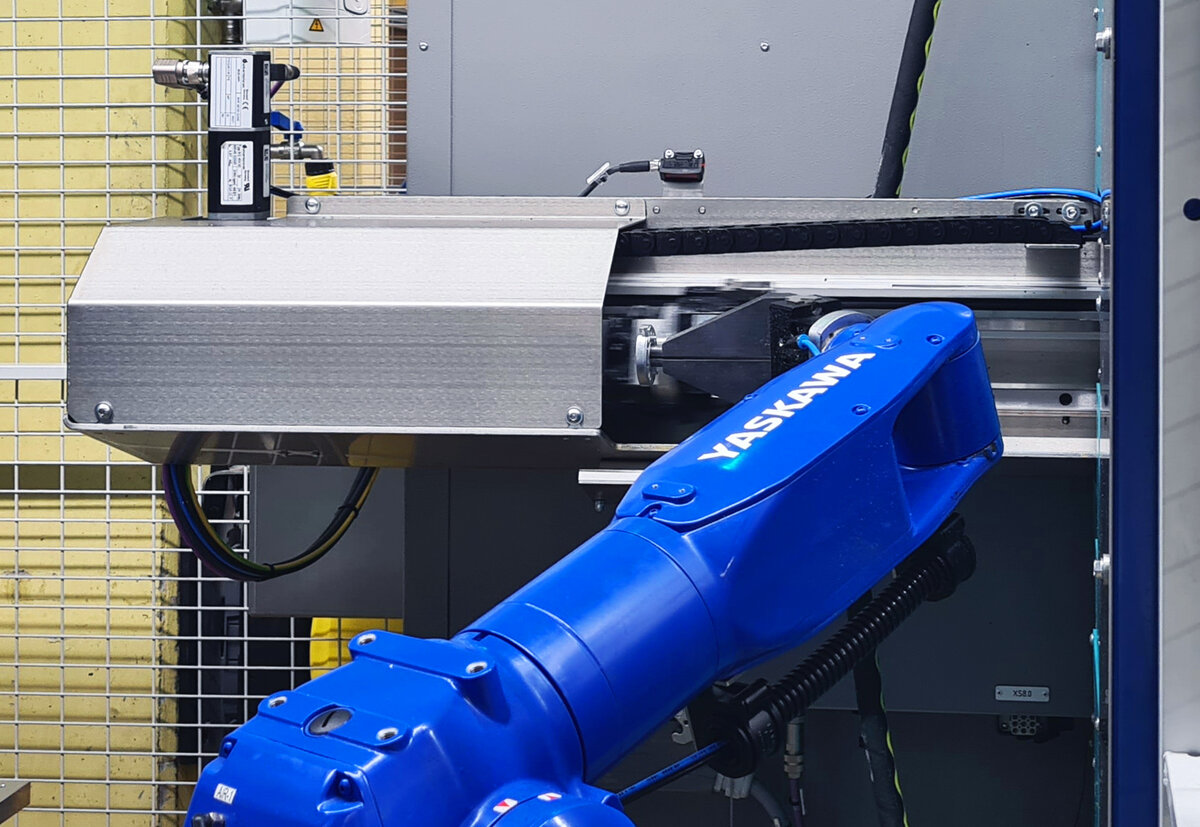
The automation in detail
At the center of the automated machining is an Index ABC lathe, which is advertised by the manufacturer as a dynamic production lathe. Prior to machining, the blanks are present as bulk material in portable mesh containers, where they are poured into a parts hopper by an operator. Via a conveyor system with pre-separation, they enter the detection area of a 3D camera from Keyence, which transmits the position of the blanks and the gripping position to the first robot in the system. This is a six-axis MOTOMAN GP7 from Yaskawa with a reach of around 900 mm and a payload of 7 kg. The radial orientation of the workpieces is also detected by the camera. A pure Bin Picking solution was not implemented, to achieve a maximum process reliability and availability, which is independent of detection difficulties and resulting malfunctions. "A very good decision", comments Koyun. "The system runs reliably and stably, and there are no malfunctions or production interruptions." The performance of Yaskawa robots already convinced Dunkermotoren in earlier production lines, which are still running stably. "Handling and adjusting programs is simple and is no problem even for our operators without robot experience after a short training," Mustafa Koyun admits.
The robot picks up the unsorted parts and transfers them to a transfer system, where they pass three tapping devices on workpiece carriers. Depending on the part variant, threads are inserted at one or more stations. The tapping units can each insert threads with different hole patterns and sizes.
After these processing steps, the workpiece carriers are returned to the first robot via the transfer system. In the transfer system, they are turned and automatically transferred to the transfer shuttle at the input of the index lathe, which feeds them to the machine.
Here, the variant-dependent machining of the total of ten end shield variants is carried out. With retooling, most of the time is spent on the machine. With automation, all that needs to be done is to select a different program and adjust the workpiece carriers of the transfer system and the gripping tools of the robots. "This is done in less than five minutes," says Koyun.
After machining is complete, the second robot, also a MOTOMAN GP7, removes the finished parts and layers them in wash baskets, where they are transported to the cleaning system and cleaned. A changeover station ensures that the baskets can be removed as and when an operator is available without interrupting the automation process. The system is already prepared install a palletizing system from the standard EGS SUMO Ecoplex2 series here at a later date, from which an AGV will pick up the baskets fully automatically and take them to the cleaning system.
The line runs completely autonomously for two to three hours, depending on the variant. The insertion of new blanks and removal of finished parts takes only a few minutes, which has reduced employee involvement to a minimum. Production takes place in two shifts. Due to the low employee commitment, an additional shift to cover short-term production peaks would be possible without any problems. Depending on the variant, the cycle time is between 15 and 35 seconds; the output is thus between 800 and 1,900 parts per shift.
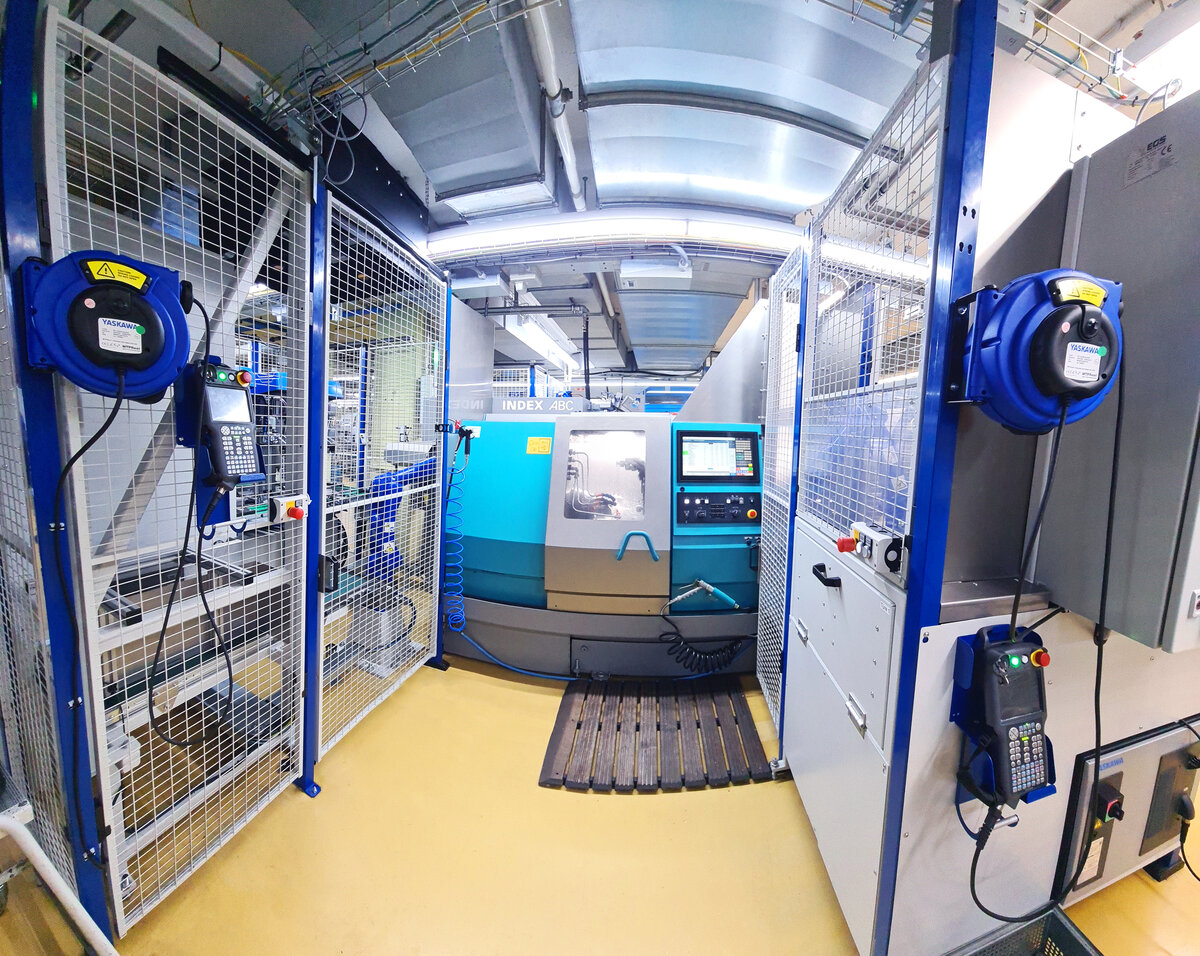
Dunkermotoren motors and EGS robots make the production plant IIoT-ready
A total of six motors from the drive technology manufacturer itself are installed in the complete plant. Brushless DC motors of the series BG perform their duties reliably on the conveyor belts of the feed system, the transfer system and the lifting units for the transfer of parts.
The integration of the smart motors are the basis for the integration of the plant into the company's digital infrastructure. Operating states of individual production components, production data and information on required maintenance were to be available online at all times. A task for the IIoT specialists from nexofox.
In addition to the recording and processing of critical machine parameters, it should be possible to record and process information from installed components. Due to the installed Dunkermotors, nexofox was able to digitize the plant itself as well as the installed motors.
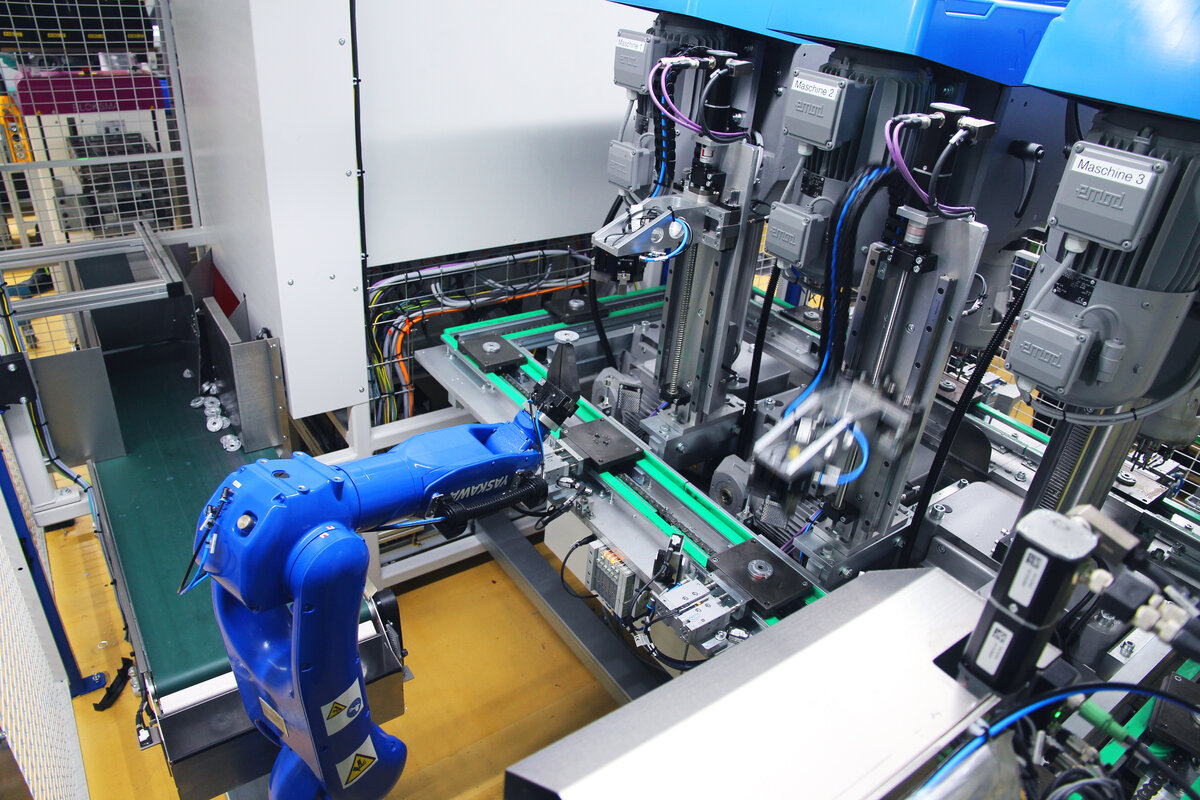
Digitized bearing shield automation
In the first step, two MOTOMAN robots from Yaskawa and three BG motors were digitized. All components were connected at the field level with an EDGE gateway. The motors were connected via the CAN protocol, while the robots were connected via PROFINET. The installed EGDE gateway connects the bearing shield automation with the cloud of Dunkermotoren and is responsible for the communication with the ERP system. The digital software solutions developed by nexofox were built on the standards of the Open Industry 4.0 Alliance (OI 4) at both the field and cloud levels. The underlying standard is defined and described in the respective Asset Administration Shells (AAS). An AAS is to be understood as a reference model that defines the format and location of data storage so that information can later be used for other assets.
The reference implementation provided by OI 4 was adapted and implemented at the field level and within the cloud. First, acquired data is used for monitoring the machine. For a fully comprehensive condition monitoring of the plant, different component parameters are used and aggregated. This then results in, for example, OEE values or the energy consumption of the bearing shield automation. With the consequent implementation of the AAS, nexofox opened up the possibility to retrieve or monitor specific parameters of the installed components. Thus, information on motor parameters such as phase current, speed or tracking error, but also important robot parameters such as cycle time, movement hours or temperature at the manipulator are available. The selection of the displayed and used parameters were discussed with Dunkermotoren in advance of the bearing shield automation and adapted to the application. Within the cloud, all parameters of the plant and the components were visualized.
Based on the condition monitoring system, third-party systems were integrated at the cloud level. The integration into the SAP maintenance software solution, for example, ensures the further processing of the data provided by nexofox. The basic idea of simple, standardized integration capability was continued in the cloud. Both SAP, also a member of OI 4, and nexofox implemented the respective implementation work on the basis of AAS, which meant that both systems could be integrated with each other without any significant effort.
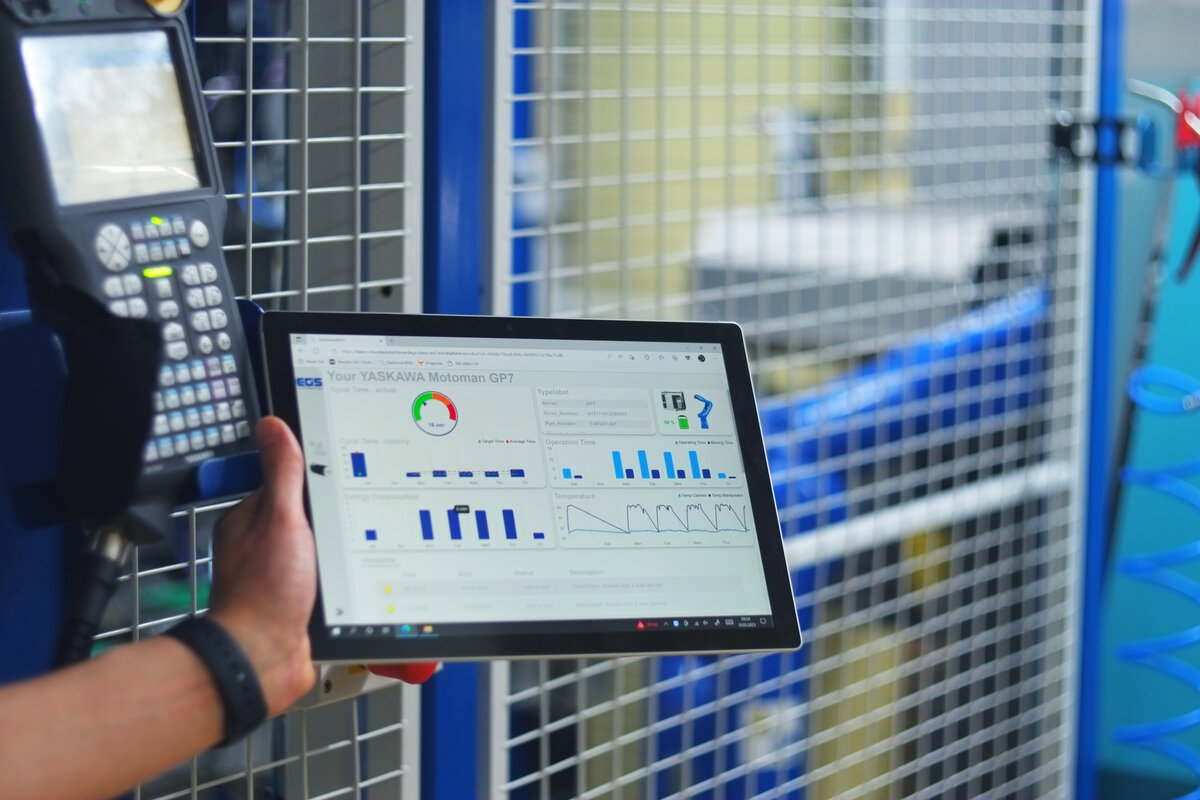
Added value thanks to digitalization
If limit values within the condition monitoring system are exceeded, Dunkermotoren is notified. Notifications are divided into messages that are not critical for production and production- or plant-critical alarms that are transmitted directly to the SAP maintenance software. For example, an alarm can be triggered by an unusually rapid rise in temperature at the manipulator. If, as here, a service call would be necessary, the data provided in the SAP maintenance software is passed on to the appropriate service technician. The app developed by nexofox could also be easily integrated into the circuit thanks to AAS and OI 4 standards. This ensures that the service technician can prepare himself optimally in the event of an assignment.
Via QR code, the plant can be identified and the service technician can be provided with the latest data. In addition to live data, all plant- and component-specific documents are also provided within the app. After completion of a service, the technician reports back the deployment via the nexofox app. The information about the completion of the assignment including activity report, as well as all service data such as duration of the assignment are reported back to the SAP maintenance software. In addition, the production planner, for example, is notified that the system is ready for production again. The alarm is acknowledged, but is available in the alarm history. This increases transparency and recurring faults can be identified more efficiently and rectified more quickly.
The first EGS plant digitized by nexofox was able to prove on several levels that a standards-based IIoT solution can be realized in less than 5 months. In addition, this application shows that the realization of a digitization solution in the Brown Field with a cooperation of different companies is easily possible thanks to simple integrability. Dunkermotoren has significantly increased its efficiency by automating the bearing shield machining and, thanks to nexofox, can fully concentrate on its core competencies even in the event of a malfunction.
This is how IIoT solutions have to be: smart - networked - cooperative – experienceable
© EGS Automation GMBH, 2023
Authors:
Heiko Röhrig, Senior Business Development Manager, EGS Automation GmbH
Christoph Baschnagel, Business Developer IIoT, nexofox/ Dunkermotoren GmbH
EGS Automation GmbH
Raiffeisenstr. 2
78166 Donaueschingen
Germany
Phone +49 771 898606-0 | Telefax: +49 771 898606-99
egs.info@ametek.com | https://www.egsautomatisierung.de/
Your contact for Public Relations:
Stefanie Tröndle
Stefanie.Troendle@ametek.com