Med den bedste robotteknologi vil vi også gerne levere til dig.
Efficient drive technology for efficient screw compressors
- Industries
- Beverages
- Fødevare
- Laboratorieautomatisering
- Applications
- Pumps & Compressors
- Client
- AquaAir
- Products
- GA70C - GA700
- SLIO
Oil-Free Compressed Air
Many sectors depend on clean compressed air. These range from the food, beverage and pharmaceuticals industries to hospitals and building technology. Further examples include laboratories and paint shops, as well as the paper processing and electrical industries. At the same time, when it comes to generating compressed air, energy efficiency is an extremely important factor in all these areas – not just for cost reasons but also in terms of ecology and sustainability. Oil-free screw compressors from AquaAir in Augsburg combined with intelligent control systems for compressed air management offer the right approach here. Powerful inverter drives, highly efficient motors and tailor-made control technology from Yaskawa play a key role in such concepts. Energy efficiency and sustainability as well as first-class technical support were persuasive arguments when it came to awarding the contract.
It is still widely believed that using oil as a lubricant in the compressor makes the process of compressing air more energy-efficient and thereby makes compressed air cheaper. Thus, every year, millions of barrels of mineral oil are used to generate compressed air and then disposed of as waste oil and oily condensate. Moreover, the oil tightness is never guaranteed. The compressed air that is contaminated with oil disperses the oil in the environment and contaminates products. This must be avoided at all costs, especially in the food or pharmaceutical industry. The effort and costs for procuring, filtering and disposing of the oil are therefore considerable, canceling out a significant portion of the envisaged energy savings. So why use oil in the compression process if oil-free compressed air is cheaper to produce and works better?
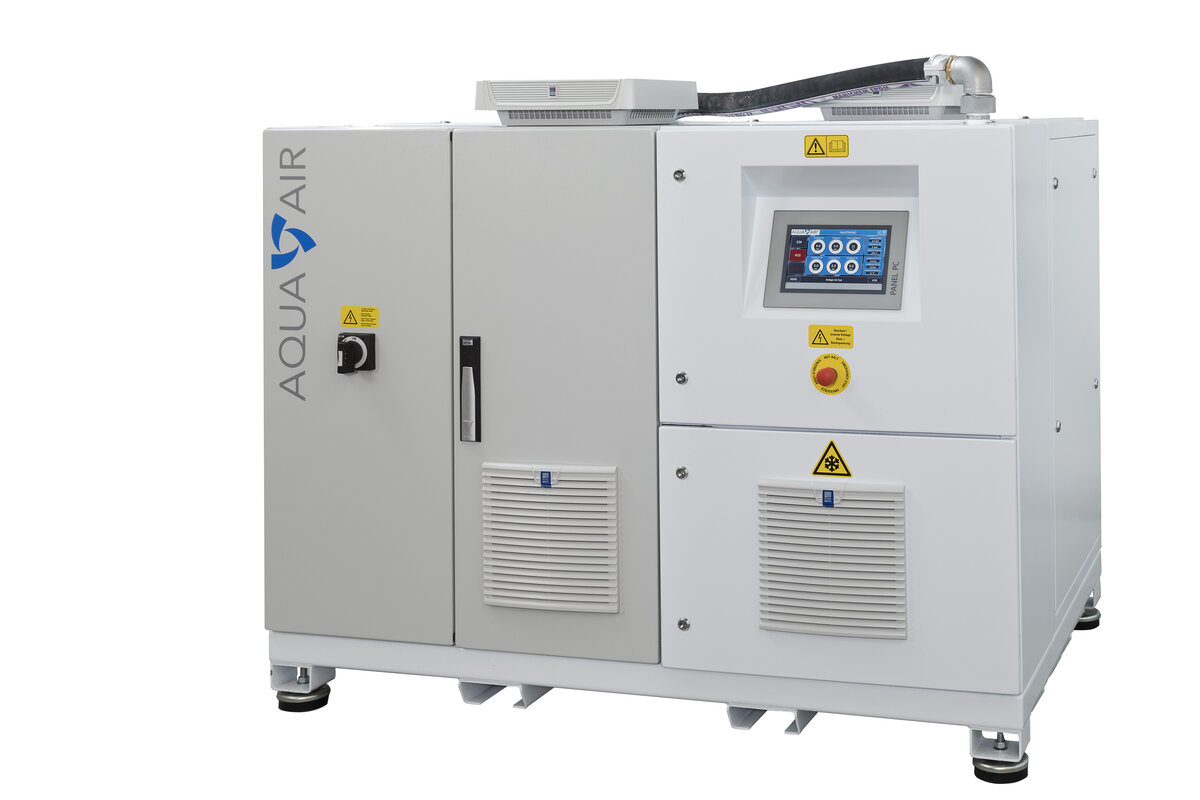
Water as a Lubricant
For several years now, the German company AquaAir has shown that there is a better way – its screw compressors, which are certified by Fresenius, use water as a lubricant and sealant instead of oil. The certified compressors are proven to be biocompatible and deliver 100% oil-free and germ-free compressed air. The compressors are extremely energy efficient and do not experience any loss of efficiency due to wear over their entire service life. They can save up to 35% in energy costs compared to conventional solutions for generating compressed air.
This is largely thanks to the innovative screw rotors, which are made from newly developed high-performance polymers. In 2018, this sustainable and ecologically designed technology was crowned with the Bavarian Innovation Award, “Innovationspreis Bayern.” The oil-free screw compressors “Made in Germany” are available in a finely graduated range of products, as a frequency-controlled system with a drive power from 4 to 110 kW, a volume flow from 0.3 to 20 m³/min and an ultimate operating pressure of between 5 and 15 bar. They also feature a powerful and user-friendly control system that can be conveniently operated by touch panel. Accordingly, the compressors boast a broad range of uses that spans industrial applications, compressed air supply in breweries, the production of vaccines as well as in medical devices, such as those used for ventilation. The oil-free compressors from Augsburg are even used at the UN headquarters in Geneva, Switzerland!
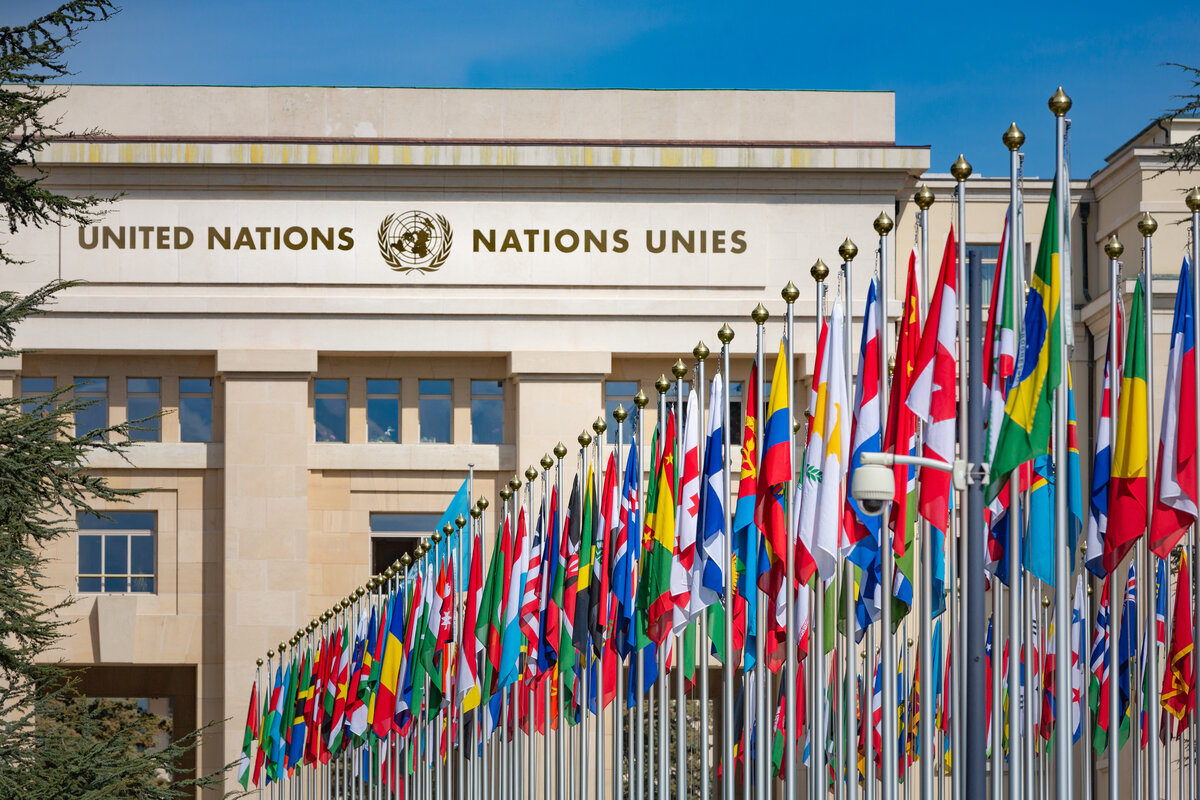
Speed Control Saves Energy
“Energy is always required when generating compressed air. But simply using a speed control system with inverter drives in place of gear units or valves provides enormous savings potential,” explains Marco Lodni, Managing Director at AquaAir. The manufacturers of the oil-free compressors have worked closely with Yaskawa on their energy-saving concept from the outset and, since 2016, the automation specialist has been the main supplier, not only for inverter drives, but also for the compact controllers and touch panels. Lodni explains the reasons for this: “Energy efficiency and sustainability are just as important to Yaskawa as they are to us. The company also boasts decades of experience with inverter drives and their use in compressors, as well as offering excellent support. This pays for itself particularly when developing customer-specific solutions and software adaptations.”
The success of the cooperation can also be seen in the compressors for generating breathing air. The partners developed the software for this medical application together, and Yaskawa supported the entire validation process with its expertise and manpower. As Lodni adds, “What’s more, we have an automation specialist on board who is also very well positioned internationally and can guarantee on-site support for our customers the world over.”
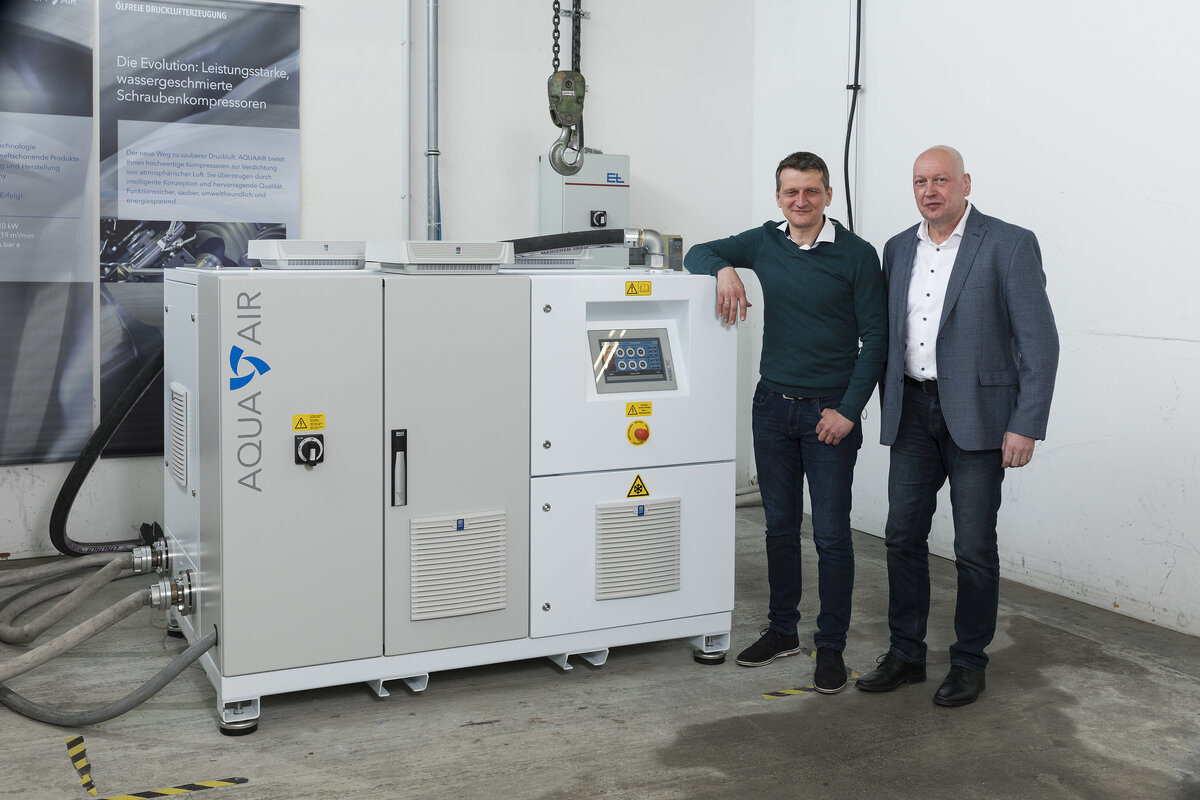
Complete Solution from a Single Source
When it came to selecting the inverter drives for the oil-free compressors, the decision was made in favor of the GA700 series. The compact inverters cover all the power levels required for the compressors, from 4 to 220 kW, and achieve efficiencies of up to 98.5%. In addition to this, they optimize the motor efficiency fully automatically, irrespective of the load or speed. The electronic speed control system means that there are also fewer moving parts on the compressors, which makes their operation very low wear. The inverters are suitable for asynchronous, permanent magnet and reluctance motors. The energy-efficient drive solution can be used for both stand-alone systems and for systems with networked drives or applications that require an increased level of safety. With a fieldbus interface card in just one inverter, up to five GA700 inverter drives can be networked. This significantly lowers costs and minimizes the wiring work required. The integrated STO function (safe torque off) means the inverters are also suitable for applications that require a safety level up to SIL3/Ple. A 24 V interface can be used to add additional sensors, such as pressure or temperature sensors. Despite boasting so many features, the inverters can still be put into operation in just a few minutes thanks to their intuitive operating concept.
Compact Yaskawa control systems from the SLIO series are used to control the inverter drives. These can be programmed in TIA, Siemens Step7 or Speed7Studio and their modular design means they can be adapted to suit the particular application. To ensure convenient operation of the compressors, the Yaskawa controller was fitted with a smart HMI. The panels are designed specifically for small to medium-size applications. Their 7-inch display not only enables menu-guided operation, but also allows visualization. When it comes to large compressor systems, the IPC series provides a powerful industrial PC with a touch panel. The combination of high-quality components and expert personal support while adapting the solutions to the specific requirements made Yaskawa the perfect partner. “We always have a complete functional solution for our oil-free compressors from a single source,” concludes Lodni.
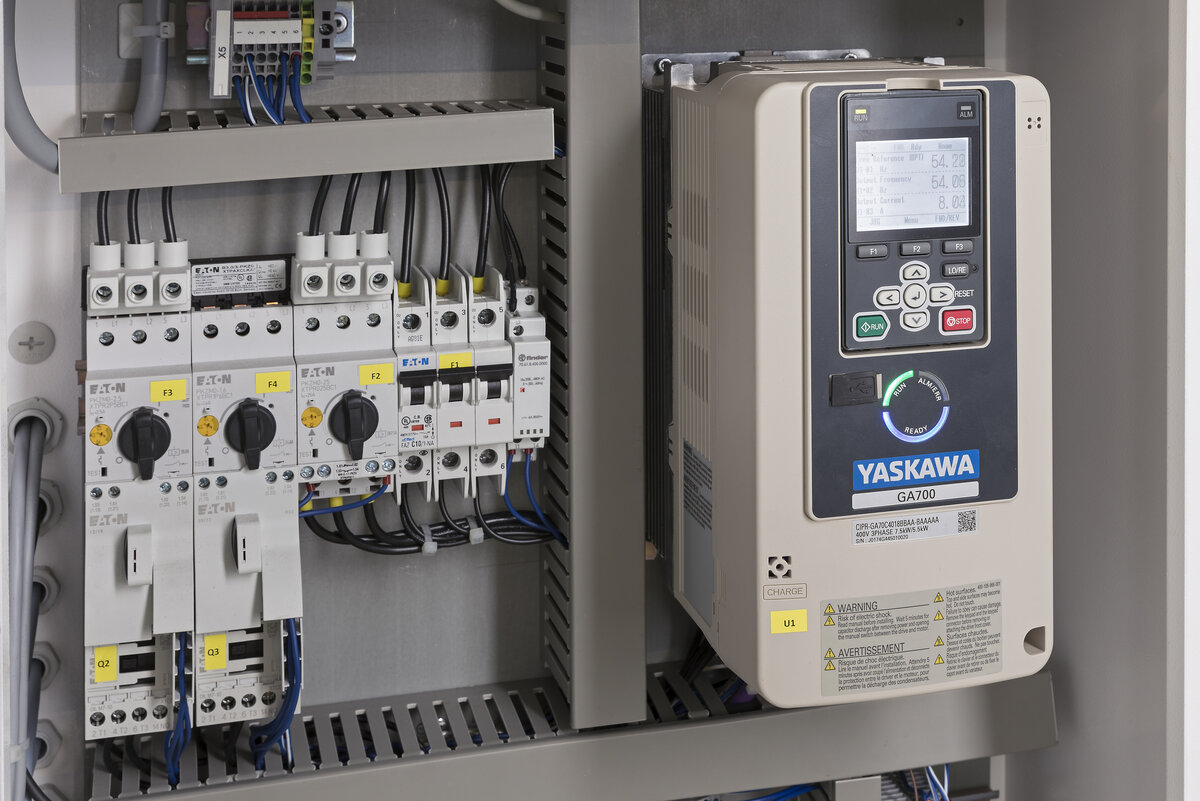