Med den bedste robotteknologi vil vi også gerne levere til dig.
Automation and robotics serving the trimming and deburring of shoe soles
Increased quality of the finished product and higher productivity. This is the summary of the goals achieved by Autec Automation in the development of a sole processing plant intended for the footwear industry. Also decisive in achieving the expected results was the performance and reliability provided by the process-integrated Yaskawa robot.
Headquartered in Ponsacco (PI) and founded in 1993, Autec Automation specializes in the design and implementation of industrial automation where improvements in production processes and a reduction in the time required to execute the process are required. It also specializes in the design, implementation of Cartesian robots and the integration of anthropomorphic robots, conveying systems, extracting, deburring and trimming parts, applying adhesives and spraying, following profiles derived off-line. Know-how and expertise made available by a team of specialists active in various engineering disciplines, able to provide high value-added automation solutions customized almost entirely for the foreign market. These include some sole trimming and deburring solutions developed for the footwear industry, in which Yaskawa robots were used.
From process requirements and criticality...
The application of trimming and deburring soles," explains the owner, Eng. Fabrizio Geri, "is both a novelty and a "mature" solution. We had produced a sole trimming plant in puliurethane about 15 years ago. In the past two years we have developed an even more advanced application that builds on our experience in the industry.
The production process of puliurethane soles, despite having applied in recent years, new technologies in some stages of the process, still involves many manual steps that slow down and fragment production as well as increase costs and reduce the quality of the finished product.
Going to analyze the various stages of the production cycle - adds Eng. Geri - it is possible to better realize the presence of manual processing in strategic points of the process that, properly automated and directly connected with the upstream and downstream stages, lead to greater linearity of production. In particular, it is the trimming/deburring operation that requires a lot of manual work, noting the poor management control at this stage.
So what, if any, problems and critical issues were encountered in the application development phase? How were they addressed and solved?
First of all," notes Eng. Geri, "it was not so immediate to be able to feed the system fully automatically, since the soles arrive at the plant all mixed in bulk in large containers. The goal was to set up a high-performance system that would be able to separate them one by one and then convey them in an oriented way to the robot work area.
Criticality, this one, solved thanks to the use of vision systems that are easily integrated with the Yaskawa control.
Secondly," continues Eng. Geri, "puliurethane soles, by the very nature of the material, cannot be handled and managed as rigid mechanical parts with precise and repeatable measurements. Their dimensions vary depending on material formulation, temperature, humidity, and so on. Therefore, it was necessary to implement online adaptive techniques made possible again by Yaskawa control.
- Industries
- Tekstil
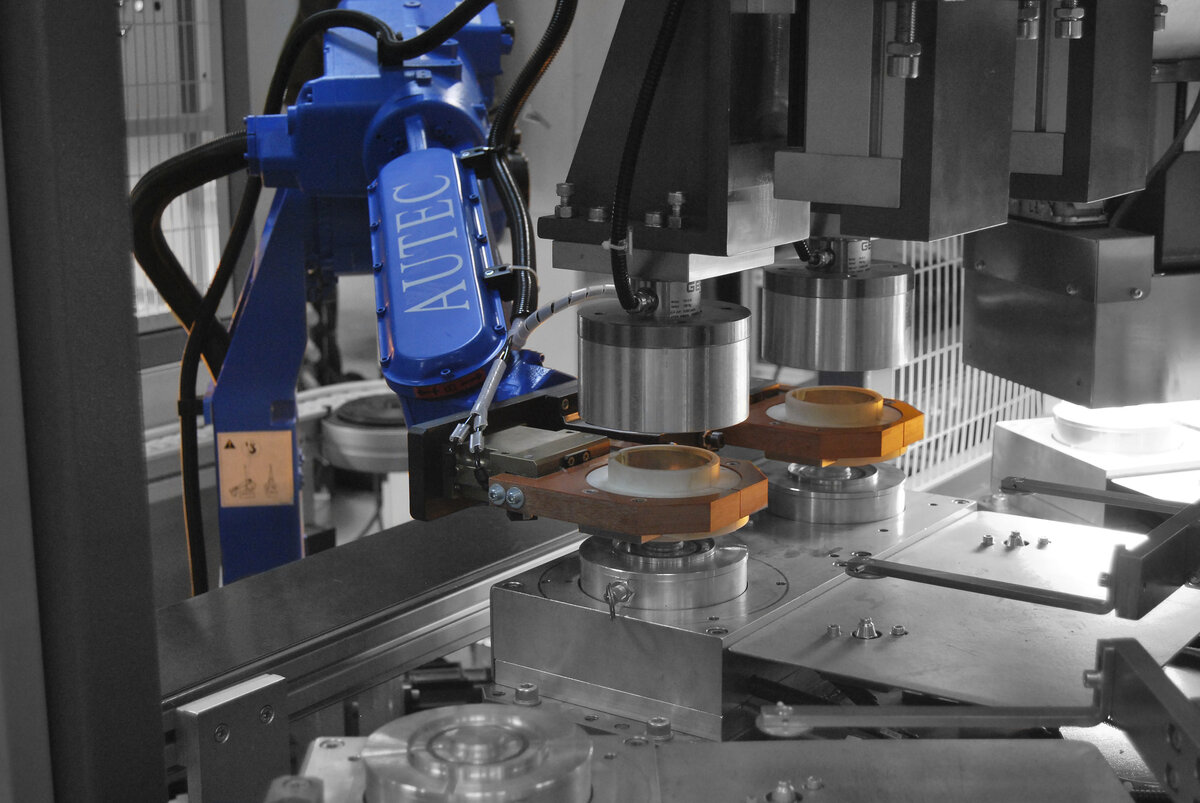
...to the operational solutions adopted...
Also key in this application to solving the problems described above was the adoption of Yaskawa Motoman MH series robots, flexible 6-axis, high-speed executions employed for a wide range of applications such as material handling and processing, machine servicing, and distribution. With payloads between 3 and 250 kg and a working area between 532 and 3,106 mm, these models feature a compact design that allows them to be positioned next to the workpiece, thus reducing cycle time.
A range," confirms Eng. Geri, "that has excellent speed characteristics, high reach, just as much precision and a very competitive price. Reason why we also make use of this type of robot in many of our other applications.
More specifically, the model chosen for the success case described in these pages is a Motoman MH-24 robot, with 6 controlled axes, a payload of up to 24 kg, a reach of up to 1,730 mm, and a positioning repeatability accuracy of 0.06 mm.
Well-defined were the requirements and technical specifications demanded of the robot and met: that it be able to be programmed off-line; that it have the ability to move the workpiece fluidly at a constant speed with respect to an external tool; that it have high axis calibration and also be extremely fast.
The fulfillment of these specifications," notes Eng. Geri, "made it possible to realize a solution to the end customer with the added value of the possibility of programming the robot without stopping production, increasing the quality of the finished product and ensuring, thanks to the appropriate dynamics, high productivity.
...to increased competitiveness
In summary, the system designed, manufactured and supplied by Autec Automation made it possible to make the operation of trimming/deburring soles fully automated.
The advantages offered by this solution," notes Eng. Geri, "concerned not only the elimination of the direct labor cost due to the trimming/deburring operation, but also the introduction of new management and control methodologies that made it possible to monitor in real time the actual progress of production, and to improve product traceability. Last but not least, the reliable control of the number of soles handled with counting and pairing of left and right soles. This aspect returns the certainty of being able to complete the production order.
As with the application example shown, in all the projects carried out by the Tuscan company, the mechanical, electrical and control design is developed completely in-house. This confirms the deep know-how acquired in almost 25 years of activity.
In Autec Automation," concludes Eng. Geri, "we have always paid great attention to innovation and research, maturing transversal skills and experience. We could almost say that our company "lives" on continuous innovation and applied research. A necessary path if the challenge is to be able to provide solutions capable of restoring productivity, efficiency, flexibility and therefore competitiveness to our customers.
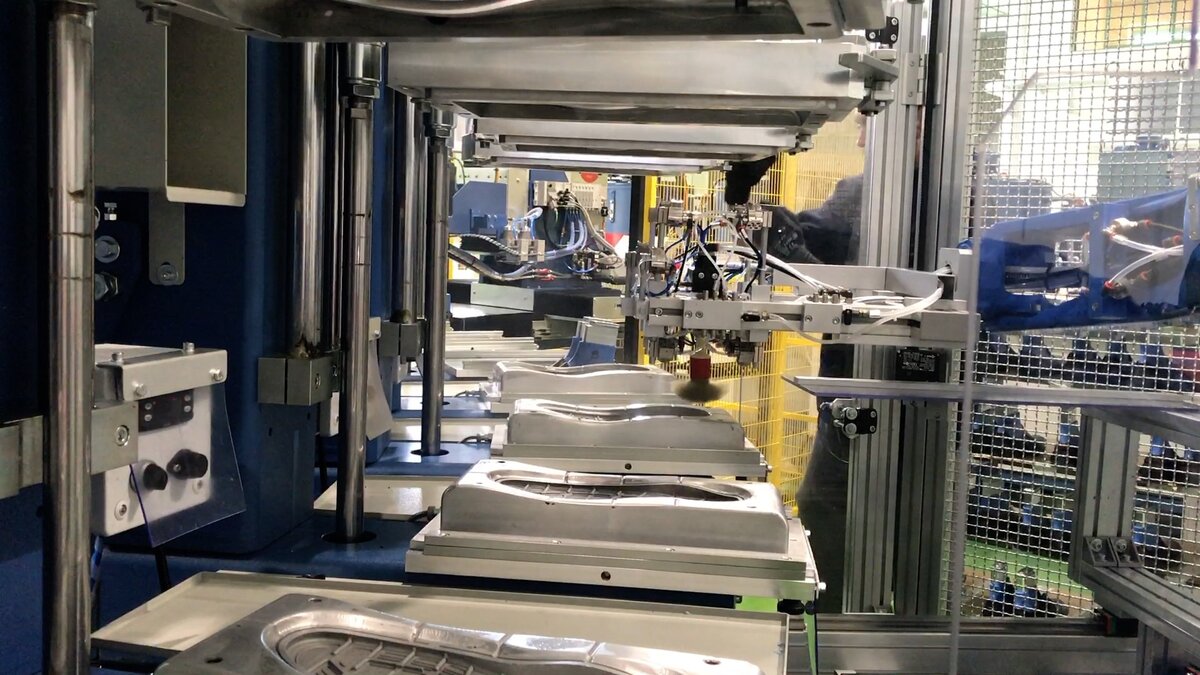